MVP Dairy, a large indoor dairy in Ohio, is creating a sustainable farming ecosystem that benefits society, the economy, and the environment. Its strategy? Thriving cows and equipment that supports a solid return on investment. In addition to employing regenerative farming to grow the food for its 4,400 cows, the dairy has been adopting electrification into its carefully organized system of checks and balances that ensures optimal cow health and farm efficiency.
In January 2024, MVP integrated Monarch’s MK-V Dairy into its daily feeding operations. This feed-pushing electric tractor supports a happy, flourishing cow herd, aligns with MVP’s sustainable farming practices, and has proven to be a cost-effective solution, boosting savings and efficiency.
Connecting the Generations
Established in 2018 and spanning two fourth-generation farming families, MVP Dairy is a partnership between the McCarty dairy farming family from Kansas and the VanTilburg grain farming family from Ohio. Not only does MVP farm for the future, but it also educates for the future of agriculture. Recognizing the disconnect between the public and modern agriculture, MVP invests in an on-site learning center to educate visitors about its dairy farming practices.
When you buy a piece of land, you buy it for the next generation to be able to use so you want to be constantly improving.
Kyle VanTilburg, Co-owner, MVP Dairy
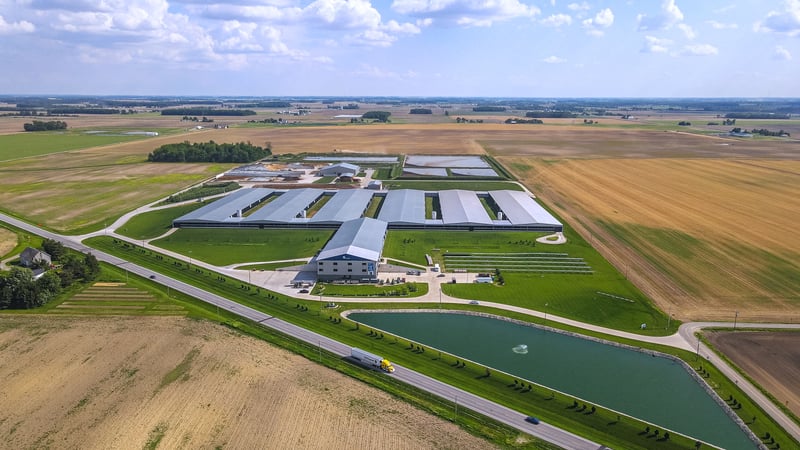
The farm operates on a circular ag economy, where crops are grown to feed the cows who in turn produce milk and manure. The milk is sold to MVP’s milk buyer, an internationally renowned company that prioritizes sustainability. The manure is used as a natural fertilizer to augment the soil and ensure a healthy crop for future feed. The farm’s water runoff is filtered through the farm’s many wetlands. An ag solar project offsets emissions and positions the dairy to produce its own energy.
24/7 Commitment to Cow Care
Dairy cows require substantial nutrition to produce milk, necessitating a round-the-clock feeding operation. At MVP the day begins at 4:30 a.m. with a specialized mixer wagon combining sustainably grown ingredients — haylage, alfalfa, corn, and soybeans. This feed is distributed along the cows' pens until 2:30 p.m. From then on, the MK-V Dairy takes over pushing feed hourly, ensuring cows have constant access to a balanced diet, even during nighttime hours. This consistent routine is crucial for maintaining cow comfort and productivity. Despite initial concerns about balancing battery life and charging time in an electric tractor, the MK-V proved to be easily integrated into the farm’s continuous operations.
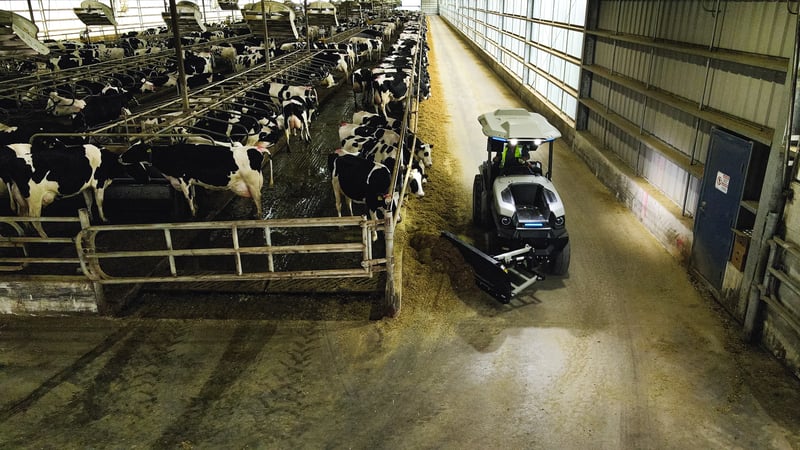
Some of the most important pieces of equipment on the farm, mechanically, are our feed loader and wagon and our Monarch feed-pushing tractor.
Brock Peters, General Manager, MVP Dairy
Savings Snapshot
The MK-V Dairy’s feed pushing trips add up. At its current rate of use to date, Peters calculates it will cover about 7,900 miles annually, the equivalent of pushing feed from California to New York and back again . . . twice. Because it’s an electric tractor, there are no emissions or associated diesel costs, which is saving the MVP thousands of dollars.
At the current pace of the hours we’re putting on it (MK-V Dairy), we’re going to be looking at about $9,500 worth of fuel savings throughout the year, which is very impressive.
Kyle VanTilburg, Co-owner, MVP Dairy
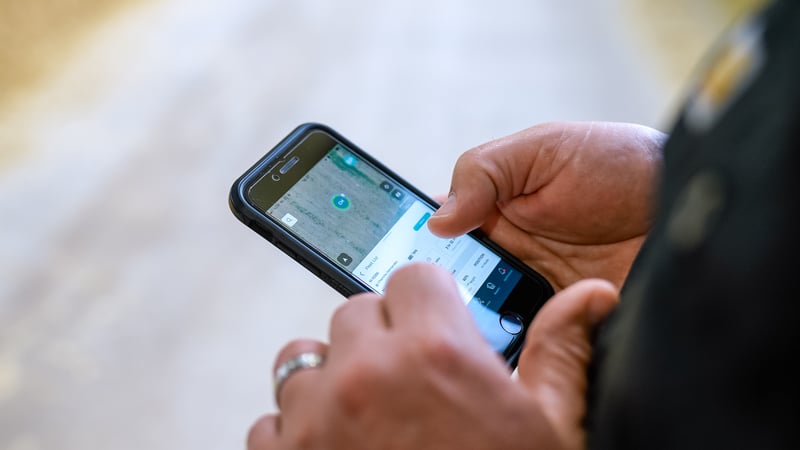
The MK-V Dairy's value extends beyond its electric powertrain. Its Wingspan Ag Intelligence (WingspanAI) web and mobile app provide crucial insights into operations, tracking metrics like usage time, energy consumption, distance traveled, average speed, fuel savings, and emissions savings. This data enables informed decision-making and helps correlate operational changes with production outcomes.
Using WingspanAI as part of MVP’s checks and balances in its feed program frees crew members to focus and manage other issues on the farm, including the all-important cow maternity ward or maintaining the six freestall pens. WingspanAI also enhances labor accountability. Peters can review historical data and video footage to identify issues affecting milk production or to ensure feeding protocols are followed consistently.
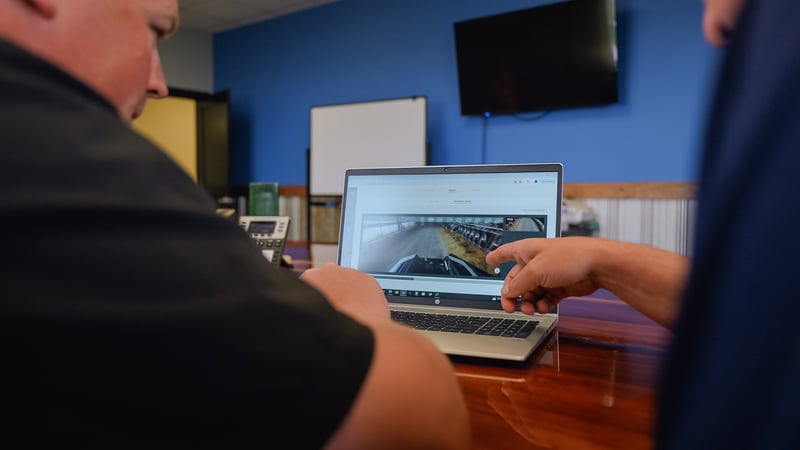
WingspanAI is huge for accountability because you can simply pull up the WingspanAI platform, show it to a team member and say, ‘Feed only got pushed five times last night. Like what happened?’
Brock Peters, General Manager, MVP Dairy
Ease of reporting is another benefit. Consumers, Peters and VanTilburg point out, vote with their dollars and want transparency of where their food originates. Generating reports easily saves time and helps strengthen MVP’s appeal to its milk purchaser to which it has a direct relationship.
“Some of their company goals kind of become our company goals,” Peters says. “We’re all striving towards the same thing and sustainability is one of those.”
In addition to supporting MVP’s exceptional cow care program, the MK-V Dairy is on track to save the dairy about 33 metric tons of CO2 annually, equivalent to removing eight gas-powered cars from the road for the year. These are compelling figures for a buyer that prioritizes sustainability and a healthy product for consumers.
Positive Production
As the dairy industry continues to evolve, MVP Dairy remains committed to continuous improvement and positive impact in communities. Its customer partnership between Monarch and use of the MK-V Dairy exemplifies its dedication to innovation and sustainability in dairy farming.